Well, didnt quite go as plan today, ended up sidetracked on the exhaust AGAIN !


more on that later in the thread....
Job No1. Fit new speedo cable. Hmmm, dash removed but it is still fiddly to get my big hands in there. I needed someone with smaller hands, fortunately my ever willing helper Matthew was on hand to do it for me. He helped me ALL day
When I`d initially drilled the hole through the bulkhead for the gearchange cables, I`d consciously moved them to the nearside to try and miss the exhaust, I`d overdone it and the left hand cable was too tightly bent, which I think was causing the catching gearchange. I drilled another hole to the right and re-routed both cables. I then wrapped the cables with fibreglass matting to stop them chafing.
I then applied silicone sealant and kneaded it into the fibreglass to hold it all in place
The passenger footbrace was fouling the cables.
1 angle grinder later.
I then made an aluminium blanking plate and riveted it over the now redundant first hole. A quick spray and it looked pretty good.
Showing the gearlever and cable routing
Matthew rebolted it into place, being smaller definately helps
Next job was to fit the rear strut bar.
Drilled the holes in the tower
Bolted it up nice and tight, Matthew being outside and holding the nut in place made a hard job easy.
I`d trimmed the wheelarches in Germany last year, but I was still not 100% with them, there was still a `lip` as you can see
5 minutes and the tool of today (angle grinder) saw this.
A quick spray with some black paint to seal it and stop any rust.
A popular `mod` is to drill the airbox, however, this also increases noise and as I am trying to ensure I dont fall foul of the very strict limits at Bedford next week, I decided to cover some of them up.
Applied silicone around the holes.
I then cut a piece of plastic to fit and applied it over the holes.
Some gaffer tape held it all in place.
Found another part of the exhaust that was blowing
My first job done from the PIT, it made it SO much easier.
Split the exhaust
Clean with some sandpaper
Nice and clean
Some exhaust cement, new U clip (coated with copperslip grease)
Oh joy of joys. I thought I`d found the leaks, nope the weld was `dripping` moisture when the car was started.
Ground off the old weld
Then rewelded to ensure it was sealed
yaay, sealed.
start it up again, hmmm, whats that noise I can hear. Oh its the exhaust blowing AGAIN
This time, it was leaking from the downpipe, where it joined the manifold. I managed to get the welding torch up close enough to seal it which was NOT easily accessible. Pit the the rescue ! Fortunately is was only a small crack and I was able to seal it
1 SEALED exhaust later, yes thats right, NO LEAKS.



I applied the heatwrap to the downpipe. I doubt I`d be able to do it from axle stands, but the Pit helped.
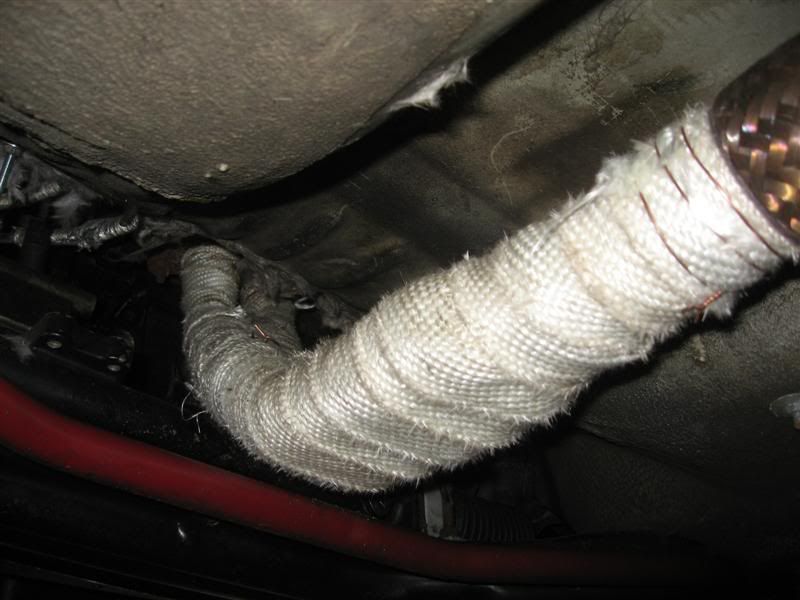